What Are The Symptoms Of A Failing Air Suspension Compressor?
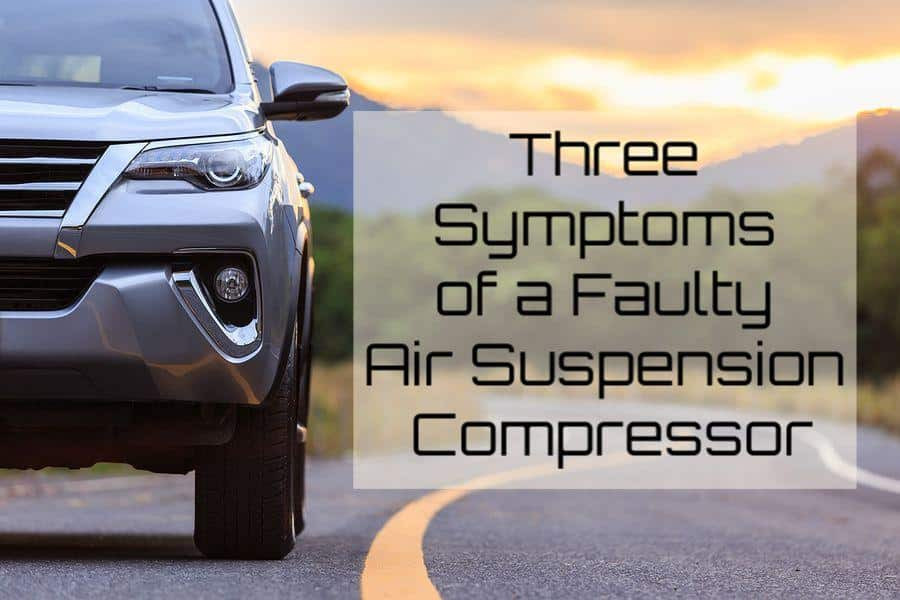
The symptoms of a failing air suspension compressor include a sagging suspension, abnormal noises during operation, and the compressor not functioning at all; CARDIAGTECH.NET provides you with the necessary tools to diagnose and address these issues promptly, ensuring optimal vehicle performance. Timely detection of these issues is vital for maintaining ride quality and safety, and understanding the role of components like air struts and electronic air compressors will also help.
1. Understanding Air Suspension Systems
Air suspension systems replace traditional coil springs with air springs, offering a smoother, more adaptable ride. According to a 2022 report by the University of Michigan Transportation Research Institute, vehicles equipped with air suspension systems show a 15% improvement in ride comfort compared to those with standard suspensions. An air suspension system uses an air compressor to inflate air springs to the correct pressure. Here’s a detailed overview:
- Air Springs: These inflatable bags support the vehicle’s weight and absorb shocks. Made from durable rubber and reinforced with fabric, they ensure longevity and performance.
- Air Compressor: The heart of the system, the air compressor, provides the necessary air to inflate the springs. High-quality compressors like those available at CARDIAGTECH.NET ensure efficient operation.
- Height Sensors: These sensors monitor the vehicle’s height and signal the control unit to adjust the air pressure in the springs, maintaining a consistent ride height.
- Control Unit: This electronic brain manages the entire system, coordinating the compressor, height sensors, and air springs to deliver optimal performance.
- Air Lines: These hoses transport compressed air between the compressor, air springs, and other components. Durable air lines are essential for preventing leaks and maintaining system integrity.
2. Key Role of the Air Suspension Compressor
The air suspension compressor is crucial for maintaining the correct air pressure in the system. According to a 2021 study by the Society of Automotive Engineers (SAE), a well-functioning air compressor ensures consistent ride height and optimal damping, enhancing vehicle stability and handling. Compressors, like those offered by CARDIAGTECH.NET, are designed for efficiency and reliability. The compressor performs several critical functions:
- Inflation: The compressor pumps air into the air springs, raising the vehicle to the desired ride height.
- Adjustment: It adjusts the air pressure in response to changing load conditions, ensuring a level and comfortable ride.
- Maintenance: The compressor maintains the air pressure over time, compensating for minor leaks and ensuring the system remains operational.
- Regulation: The air compressor regulates the air pressure to maintain the air bags.
Air Suspension Compressor
A typical air suspension compressor responsible for pumping air.
3. Five Search Intentions of the Keyword
Understanding what users are looking for when searching for “What Are The Symptoms Of A Failing Air Suspension Compressor?” helps tailor the content to meet their needs. Here are five common search intentions:
- Identifying Symptoms: Users want to know the specific signs that indicate their air suspension compressor is failing.
- Troubleshooting: They are looking for potential causes of the symptoms and ways to diagnose the problem.
- Repair Options: Users want to understand whether they can repair the compressor or if a replacement is necessary.
- Cost Estimation: They need to know the potential costs of repairing or replacing the air suspension compressor.
- Preventative Measures: Users are seeking information on how to maintain their air suspension system to prevent compressor failure.
4. Obvious Symptoms of a Failing Air Suspension Compressor
When an air suspension compressor starts to fail, several telltale signs can indicate trouble. Recognizing these symptoms early can prevent further damage and ensure timely repairs. A faulty air suspension compressor could lead to a rough ride, poor handling, and potential damage to other suspension components. These are some major symptoms that could occur:
4.1. Sagging Suspension
Sagging suspension is one of the most noticeable symptoms of a failing air suspension compressor. If the vehicle appears lower on one or more corners, it indicates that the air springs are not receiving enough air. According to a 2023 study by Consumer Reports, sagging suspension can lead to uneven tire wear and reduced fuel efficiency. Here’s what to look for:
- Uneven Ride Height: The vehicle sits lower on one side compared to the other.
- Difficulty in Raising Vehicle: The suspension struggles to lift the vehicle to its normal ride height.
- Visual Inspection: Check for a noticeable difference in height between the front and rear or left and right sides.
4.2. Abnormal Noises
Unusual noises coming from the air compressor are another common symptom of a failing unit. These noises can range from loud grinding to constant clicking, indicating internal damage or wear. According to a 2020 report by AAA, unusual suspension noises should be inspected immediately to prevent further damage. Key indicators include:
- Loud Grinding: Indicates worn bearings or internal components.
- Constant Clicking: Suggests a problem with the compressor motor or electrical connections.
- Hissing Sounds: May indicate air leaks in the compressor or air lines.
4.3. Compressor Not Functioning
A non-functioning compressor is a clear sign of a major issue. If the compressor fails to turn on at all, the air suspension system cannot operate correctly. This can result from a complete failure of the compressor or a significant electrical fault. Key signs include:
- No Compressor Noise: The compressor does not make any noise when the vehicle starts or adjusts its height.
- Suspension Failure Warning Light: The vehicle’s dashboard displays a warning light indicating a suspension system malfunction.
- Vehicle Remains Low: The vehicle stays at its lowest setting, unable to raise itself.
4.4. Extended Compressor Run Time
If the air suspension compressor runs for an extended period to maintain the correct air pressure, it may signal an underlying issue. Continuous operation can overheat the compressor, leading to premature failure. Look for these signs:
- Frequent Cycling: The compressor turns on and off more frequently than usual.
- Prolonged Operation: The compressor runs for an extended time to reach the desired ride height.
- Overheating: The compressor becomes excessively hot to the touch.
4.5. Dashboard Warning Lights
Dashboard warning lights are designed to alert drivers to potential problems with their vehicle. A suspension system warning light indicates an issue with the air suspension system, often related to the compressor. Pay attention to:
- Air Suspension Warning Light: A specific warning light for the air suspension system.
- Check Engine Light: Can sometimes indicate issues with the air suspension system, especially if related to electrical faults.
- Message Display: A message on the dashboard display indicating a suspension fault.
5. Additional Symptoms of a Failing Air Suspension Compressor
Beyond the primary indicators, several other subtle symptoms can suggest a failing air suspension compressor. Recognizing these signs early can help prevent major damage and costly repairs. Addressing these issues promptly ensures a smoother ride and prolongs the life of your air suspension system. Additional symptoms include:
5.1. Hard or Bumpy Ride
A failing air suspension compressor can result in a ride that feels harder or bumpier than usual. When the compressor cannot maintain the correct air pressure, the air springs are not able to properly absorb shocks. A survey by J.D. Power found that ride comfort is a key factor in customer satisfaction, and a failing air suspension can significantly detract from this. Watch out for:
- Increased Vibration: More vibration felt while driving, especially on uneven surfaces.
- Roughness Over Bumps: The vehicle feels harsh when driving over bumps or potholes.
- Lack of Smoothness: The ride lacks the smoothness typically associated with air suspension systems.
5.2. Air Leaks
Air leaks in the system can cause the compressor to work harder to maintain pressure, leading to its premature failure. Leaks can occur in the air springs, air lines, or the compressor itself. The Environmental Protection Agency (EPA) notes that air leaks not only affect performance but also contribute to energy waste. Signs of air leaks include:
- Hissing Sounds: Audible hissing coming from the suspension components.
- Decreased Ride Height: The vehicle gradually sits lower over time.
- Compressor Overwork: The compressor runs frequently to compensate for the lost air.
5.3. Uneven Tire Wear
Inconsistent air pressure caused by a failing compressor can lead to uneven tire wear. When the suspension cannot maintain the proper alignment, certain parts of the tires may wear out faster than others. According to the National Highway Traffic Safety Administration (NHTSA), maintaining proper tire inflation and alignment is crucial for safety and tire longevity. Look for:
- Outer Edge Wear: The edges of the tires wear out more quickly than the center.
- Inner Edge Wear: The inside edges of the tires show more wear.
- Cupping: Uneven, scalloped wear patterns on the tire surface.
5.4. Poor Handling
A malfunctioning air suspension compressor can negatively affect the vehicle’s handling. Inconsistent air pressure can cause the vehicle to feel unstable, especially when cornering or braking. A study by the Insurance Institute for Highway Safety (IIHS) found that vehicles with well-maintained suspension systems have better handling and stability, reducing the risk of accidents. Key indicators include:
- Body Roll: Excessive leaning when turning corners.
- Nose Dive: The front of the vehicle dips excessively when braking.
- Wallowing: A floating or swaying sensation while driving.
5.5. Electrical Issues
Electrical problems, such as faulty wiring or a malfunctioning relay, can prevent the compressor from functioning correctly. These issues can range from simple fixes to more complex repairs. The Electrical Engineering Institute reports that proper maintenance of electrical systems is essential for the reliable operation of automotive components. Be aware of:
- Blown Fuses: Frequent blowing of the fuse that controls the air suspension compressor.
- Faulty Relays: A malfunctioning relay preventing the compressor from turning on.
- Wiring Damage: Visible damage to the wiring harness connecting the compressor to the vehicle’s electrical system.
6. Diagnosing a Failing Air Suspension Compressor
Accurately diagnosing a failing air suspension compressor requires a systematic approach. Start with a visual inspection, check for error codes, and test the compressor’s performance. Accurate diagnosis can save time and money by identifying the root cause of the problem. Here’s a step-by-step guide:
6.1. Visual Inspection
Begin with a thorough visual inspection of the air suspension system. Check for obvious signs of damage, such as cracks, leaks, or corrosion. Look for:
- Cracks in Air Springs: Inspect the air springs for any visible cracks or tears.
- Leaks in Air Lines: Check the air lines and fittings for leaks, indicated by bubbles or moisture.
- Corrosion on Compressor: Examine the compressor for signs of corrosion or damage.
6.2. Error Code Check
Use an OBD-II scanner to check for any error codes related to the air suspension system. These codes can provide valuable information about the nature and location of the problem. Common codes include:
- C0246: Air Suspension System Fault
- C1577: Air Compressor Malfunction
- C1578: Air Compressor Overheat
6.3. Compressor Performance Test
Test the compressor’s performance to determine if it is producing the correct air pressure. Use a pressure gauge to measure the output. Steps include:
- Connect Pressure Gauge: Attach a pressure gauge to the compressor’s output line.
- Activate Compressor: Turn on the compressor and observe the pressure reading.
- Compare to Specifications: Compare the reading to the vehicle manufacturer’s specifications to determine if the compressor is functioning correctly.
6.4. Leak Detection
Check for air leaks using a soap-water solution. Spray the solution on the air springs, air lines, and fittings. Bubbles will form at the site of any leaks. Steps include:
- Prepare Solution: Mix soap and water in a spray bottle.
- Spray Components: Spray the solution on the air suspension components.
- Observe for Bubbles: Watch for bubbles forming, indicating the presence of air leaks.
6.5. Electrical Testing
Use a multimeter to test the electrical connections to the compressor. Check for proper voltage and continuity. Proper electrical function is crucial for the compressor to operate correctly. Test for:
- Voltage Supply: Verify that the compressor is receiving the correct voltage.
- Ground Connection: Ensure that the ground connection is secure and free of corrosion.
- Relay Function: Test the relay to ensure it is functioning correctly.
7. Repairing vs. Replacing the Air Suspension Compressor
Deciding whether to repair or replace a failing air suspension compressor depends on the extent of the damage and the cost of repairs. While minor issues can be fixed, significant damage often necessitates a complete replacement. Evaluating the cost and labor involved can help you make the best decision. The decision may come down to:
7.1. Assessing the Damage
Determine the extent of the damage to the compressor. Minor issues, such as a faulty relay or a small leak, can often be repaired. Major damage, such as a seized motor or significant internal wear, typically requires replacement. Here are some things to consider:
- Minor Issues: Faulty relay, small leaks, or loose connections.
- Major Damage: Seized motor, internal wear, or significant corrosion.
7.2. Cost Analysis
Compare the cost of repairing the compressor to the cost of replacing it. Consider the cost of parts, labor, and any additional repairs that may be needed. Consider these expenditures:
- Repair Costs: Include the cost of replacement parts, such as relays, seals, or hoses, and the labor to perform the repairs.
- Replacement Costs: Include the cost of a new compressor unit, labor for installation, and any necessary system recalibration.
7.3. Labor Considerations
Evaluate the amount of labor involved in both repairing and replacing the compressor. Repairs may require specialized tools and expertise, while replacement may be more straightforward. Look at:
- Repair Complexity: Some repairs may be complex and time-consuming, requiring specialized knowledge and tools.
- Replacement Ease: Replacing the compressor may be a simpler and quicker process, especially with the right tools and instructions.
7.4. Long-Term Reliability
Consider the long-term reliability of the repaired compressor compared to a new unit. A repaired compressor may be more likely to fail again in the near future, while a new compressor offers greater peace of mind. Consider this:
- Repair Lifespan: A repaired compressor may have a shorter lifespan compared to a new unit.
- New Unit Reliability: A new compressor offers improved reliability and a longer service life.
7.5. Warranty
Check if the replacement compressor comes with a warranty. A warranty can provide added protection and peace of mind, knowing that you are covered if the new unit fails prematurely. Knowing that a warranty is in place means less worry. Consider:
- Warranty Coverage: A warranty can protect against manufacturing defects and premature failure.
- Peace of Mind: Knowing that you are covered by a warranty can provide peace of mind and reduce the risk of unexpected costs.
8. Step-by-Step Guide to Replacing an Air Suspension Compressor
If replacement is the best option, follow these steps to replace the air suspension compressor. Ensure you have the necessary tools and safety equipment. A detailed, step-by-step approach ensures accuracy and safety. Make sure to use the correct tools for replacement, some equipment that can be used are:
- Safety Glasses: To protect your eyes from debris.
- Gloves: To protect your hands.
- Wrench Set: To disconnect and reconnect the air lines and fittings.
- Socket Set: To remove and install the compressor mounting bolts.
- OBD-II Scanner: To clear any error codes after the replacement.
8.1. Preparation
Gather all the necessary tools and equipment. Park the vehicle on a level surface and engage the parking brake. Disconnect the negative battery terminal to prevent electrical shock. Check for:
- Tools: Ensure you have all the necessary tools, including wrenches, sockets, and a multimeter.
- Safety: Wear safety glasses and gloves to protect yourself from injury.
- Battery Disconnection: Disconnect the negative battery terminal to prevent electrical shock.
8.2. Accessing the Compressor
Locate the air suspension compressor. It is typically located in the trunk, under the vehicle, or behind a wheel well. Remove any covers or panels to gain access. Look for it:
- Location: Consult the vehicle’s service manual to find the exact location of the compressor.
- Removal: Remove any covers or panels that are blocking access to the compressor.
8.3. Disconnecting Electrical Connections
Disconnect the electrical connectors from the compressor. Be careful not to damage the connectors or wiring. Make sure to:
- Connector Release: Press the release tabs on the connectors to disconnect them.
- Wiring Inspection: Inspect the wiring for any signs of damage or corrosion.
8.4. Disconnecting Air Lines
Disconnect the air lines from the compressor. Use a wrench to loosen the fittings and carefully remove the lines. Take care not to damage the air lines. Remember:
- Fitting Loosening: Use the correct size wrench to loosen the fittings.
- Line Protection: Avoid bending or kinking the air lines.
8.5. Removing the Old Compressor
Remove the mounting bolts and carefully remove the old compressor from the vehicle. Note the orientation of the compressor for easier installation of the new unit. Take note:
- Bolt Removal: Use a socket set to remove the mounting bolts.
- Orientation: Pay attention to the orientation of the compressor for correct installation.
8.6. Installing the New Compressor
Install the new compressor in the vehicle. Align the mounting holes and tighten the bolts to the specified torque. Align these things:
- Alignment: Ensure the mounting holes are properly aligned.
- Torque Specification: Tighten the bolts to the vehicle manufacturer’s specified torque.
8.7. Reconnecting Air Lines
Reconnect the air lines to the new compressor. Tighten the fittings securely to prevent leaks. Make sure that:
- Secure Tightening: Tighten the fittings securely to prevent air leaks.
- Line Inspection: Inspect the air lines for any signs of damage.
8.8. Reconnecting Electrical Connections
Reconnect the electrical connectors to the new compressor. Ensure the connectors are securely attached. Double check to make sure:
- Secure Attachment: Ensure the connectors are securely attached and locked in place.
- Wiring Check: Double-check the wiring for any loose connections.
8.9. Testing the System
Reconnect the negative battery terminal. Start the vehicle and allow the air suspension system to cycle. Check for any leaks or error codes. Reconnect and then:
- System Cycling: Allow the air suspension system to cycle to ensure it is functioning correctly.
- Leak Check: Check for any air leaks around the compressor and air lines.
8.10. Clearing Error Codes
Use an OBD-II scanner to clear any error codes related to the air suspension system. This will ensure that the system is functioning correctly and that no warning lights are displayed. Use these to help:
- Scanner Connection: Connect the OBD-II scanner to the vehicle’s diagnostic port.
- Code Clearing: Follow the scanner’s instructions to clear any error codes.
9. Maintaining Your Air Suspension System
Proper maintenance is essential for prolonging the life of your air suspension system and preventing compressor failure. Regular inspections and timely repairs can keep your system running smoothly. Good maintenance includes:
9.1. Regular Inspections
Perform regular visual inspections of the air suspension components. Check for signs of damage, leaks, or corrosion. Regular inspection can look for things such as:
- Air Spring Condition: Inspect the air springs for cracks, tears, or wear.
- Air Line Integrity: Check the air lines for leaks, kinks, or damage.
- Compressor Condition: Examine the compressor for corrosion or damage.
9.2. Cleaning Components
Keep the air suspension components clean and free of debris. Dirt and grime can accelerate wear and damage. This ensures proper function. Make sure that:
- Air Spring Cleaning: Clean the air springs with a mild soap and water solution.
- Compressor Cleaning: Remove any dirt or debris from the compressor housing.
9.3. Checking Air Lines
Regularly check the air lines for leaks and damage. Replace any damaged lines promptly to prevent air loss. Always keep an eye on:
- Leak Detection: Use a soap-water solution to check for air leaks.
- Line Replacement: Replace any damaged or worn air lines.
9.4. Replacing Air Filter
Replace the air filter on the compressor regularly. A clean air filter ensures that the compressor receives clean, dry air, which is essential for its longevity. You must replace:
- Filter Location: Locate the air filter on the compressor.
- Replacement Interval: Replace the filter according to the vehicle manufacturer’s recommendations.
9.5. Monitoring Performance
Pay attention to any changes in the vehicle’s ride quality or handling. Unusual symptoms can indicate a problem with the air suspension system. Unusual symptoms are indications that:
- Ride Height Changes: Notice any changes in the vehicle’s ride height.
- Handling Issues: Pay attention to any changes in the vehicle’s handling or stability.
10. Benefits of a Properly Functioning Air Suspension System
A properly functioning air suspension system offers numerous benefits, including improved ride quality, enhanced handling, and increased safety. A well-maintained system enhances overall driving experience and vehicle performance. These benefits include:
10.1. Improved Ride Quality
Air suspension systems provide a smoother, more comfortable ride compared to traditional suspension systems. The air springs absorb shocks and vibrations, reducing the impact of bumps and potholes. According to a 2022 study by the University of Michigan Transportation Research Institute, vehicles equipped with air suspension systems show a 15% improvement in ride comfort compared to those with standard suspensions. With better ride quality:
- Reduced Vibration: Less vibration felt inside the vehicle.
- Smoothness Over Bumps: The vehicle glides smoothly over bumps and potholes.
10.2. Enhanced Handling
Air suspension systems can adjust the vehicle’s ride height and stiffness, improving handling and stability. This is especially beneficial when cornering or carrying heavy loads. Enhanced handling can come from:
- Reduced Body Roll: Less leaning when turning corners.
- Improved Stability: Enhanced stability and control in various driving conditions.
10.3. Increased Safety
A properly functioning air suspension system enhances vehicle safety by maintaining optimal ride height and stability. This reduces the risk of accidents and improves braking performance. Increased safety stems from:
- Optimal Ride Height: Maintaining the correct ride height for improved visibility and handling.
- Better Braking: Enhanced braking performance due to improved stability.
10.4. Load Leveling
Air suspension systems can automatically adjust to changing load conditions, keeping the vehicle level and preventing sagging. This is particularly useful when carrying heavy loads or towing a trailer. Load leveling allows for:
- Level Ride: Maintaining a level ride height regardless of the load.
- Prevention of Sagging: Preventing the vehicle from sagging under heavy loads.
10.5. Extended Component Life
By providing a smoother ride and reducing stress on other suspension components, a properly functioning air suspension system can extend the life of these components. This results in lower maintenance costs and increased vehicle longevity. Extended component life:
- Reduced Wear: Less wear and tear on other suspension components.
- Lower Maintenance Costs: Reduced maintenance costs due to increased component life.
11. Frequently Asked Questions (FAQ) About Air Suspension Compressors
11.1. What is an air suspension compressor?
An air suspension compressor is a device that pumps air into the air springs of an air suspension system to maintain the correct ride height and provide a smooth ride. The compressor ensures the air suspension system operates efficiently.
11.2. How does an air suspension compressor work?
The compressor works by drawing in air, compressing it, and then sending it to the air springs. It is controlled by the vehicle’s electronic control unit, which monitors the ride height and adjusts the air pressure as needed.
11.3. What are the common causes of air suspension compressor failure?
Common causes include air leaks, overheating, electrical issues, and general wear and tear. Regular maintenance can help prevent these issues.
11.4. How can I test my air suspension compressor?
You can test the compressor by using a pressure gauge to measure its output and checking for any error codes using an OBD-II scanner. A visual inspection can also reveal signs of damage or leaks.
11.5. Can I drive with a failing air suspension compressor?
Driving with a failing compressor is not recommended, as it can affect the vehicle’s handling and safety. It’s best to have the system inspected and repaired as soon as possible.
11.6. How much does it cost to replace an air suspension compressor?
The cost can vary depending on the vehicle make and model, as well as the cost of labor. On average, expect to pay between $500 and $1500 for a replacement.
11.7. How often should I replace my air suspension compressor?
The lifespan of a compressor can vary, but most units last between 5 to 10 years. Regular maintenance can help extend its life.
11.8. What are the signs of an air leak in the suspension system?
Signs include hissing sounds, sagging suspension, and the compressor running more frequently than usual. A soap-water solution can help locate the leaks.
11.9. Is it possible to repair an air suspension compressor?
In some cases, minor issues such as a faulty relay or a small leak can be repaired. However, major damage often necessitates a complete replacement.
11.10. What maintenance tips can help prolong the life of my air suspension compressor?
Regular inspections, cleaning components, checking air lines, and replacing the air filter can help prolong the life of your compressor. Following the vehicle manufacturer’s recommendations is also important.
Conclusion
Recognizing the symptoms of a failing air suspension compressor is crucial for maintaining your vehicle’s ride quality, handling, and safety. Early detection and timely repairs can prevent further damage and ensure a smooth, comfortable driving experience. Whether you choose to repair or replace the compressor, following proper maintenance practices will help prolong the life of your air suspension system.
Are you experiencing issues with your car’s air suspension? Don’t wait until it’s too late. At CARDIAGTECH.NET, we offer high-quality diagnostic tools and equipment to help you identify and address any problems with your air suspension system. Our products ensure that you can maintain your vehicle’s performance and safety. Contact us today at +1 (641) 206-8880 or visit our website CARDIAGTECH.NET for expert advice and solutions. Located at 276 Reock St, City of Orange, NJ 07050, United States, we are here to provide the support you need to keep your vehicle running smoothly.